All paints are basically similar in composition in that they contain a suspension of finely ground solids (pigments) in a liquid medium (vehicle) consisting of a polymeric or resinous material (binder) and a volatile solvent.
With a brush, a roller, or a spray gun, paint is applied in a thin coat to various surfaces such as wood, metal, or stone. Paint is used to decorate, protect and prolong the life of natural and synthetic materials, and acts as a barrier against environmental conditions. Paints may be broadly classified into Decorative paints, applied on site to decorate and protect buildings and other objects, and Industrial coatings which are applied in factories to finish manufactured goods such as cars.[1]
The constituents of paint:
Paints contain:
- Pigment(s) -
prime pigments to impart colour and opacity
- Binder
(resin) - a polymer, often referred to as resin, forming a matrix to hold
the pigment in place
- Extender -
larger pigment particles added to improve adhesion, strengthen the film
and save binder
- Solvent
(sometimes called a thinner) - either an organic solvent or water is used
to reduce the viscosity of the paint for better application. Water-borne
paints are replacing some paints that use volatile organic compounds such
as the hydrocarbons which are harmful to the atmosphere.
- Additives -
used to modify the properties of the liquid paint or dry film
The binder (resin) and
solvent together are sometimes known as the vehicle. The binder may be
dissolved as a solution or carried as a dispersion of microscopically small
particles in a liquid.
Depending on the type of
paint and intended use, additives may include:
- dispersants
- to separate and stabilise pigment particles
- silicones -
to improve weather resistance
- thixotropic
agents - to give paints a jelly-like consistency that breaks down to a
liquid when stirred or when a brush is dipped into it
- driers - to
accelerate drying time
- anti-settling
agents - to prevent pigment settling
- bactericides
- to preserve water based paints in the can
- fungicides
and algaecides - to protect exterior paint films against disfigurement
from moulds, algae and lichen
Paints are formulated according to their proposed use - primer,
undercoat, special finishes (matt, gloss, heat resistance, anti-corrosion,
abrasion resistance).[2]
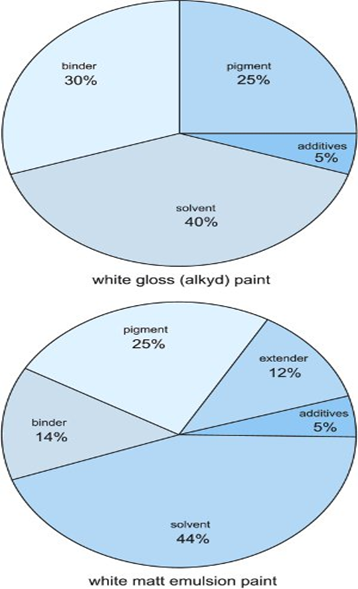
Figure 1:
Contents of a white gloss (alkyd) paint and a white matt emulsion (acrylic)
paint.
Properties of an ideal paint:
These
vary greatly according to the particular end use. The requirements for an
automotive topcoat, for example, will be very different to those for a
decorative ceiling paint.
Some
of the typical attributes required can include:
- ease of
application
- good flow
out of application marks (e.g. brush-marking)
- forming a
continuous protective film
- high opacity
- quick drying
- corrosion resistance
- water
resistance
- heat resistance
- color stability (i.e. against visible and ultraviolet radiation)
- abrasion and scratch resistance
- durability
- flexibility
- easily cleaned
Manufacturing:
Raw Materials:
A
paint is composed of
Ø pigments
(Hundreds of different pigments, both natural and synthetic, exist. The basic
white pigment is titanium dioxide, selected for its excellent concealing
properties, and black pigment is commonly made from carbon black. Other
pigments used to make paint include iron oxide and cadmium sulfide for reds,
metallic salts for yellows and oranges, and iron blue and chrome yellows for
blues and greens.)
Ø solvents
(They include petroleum mineral spirits and aromatic solvents such as benzol,
alcohols, esters, ketones, and acetone)
Ø resins
(The natural resins most commonly used are lin-seed, coconut, and soybean oil,
while alkyds, acrylics, epoxies, and polyurethanes number among the most
popular synthetic resins.)
Ø various
additives. (Some, like calcium carbonate and aluminum silicate) [1]
Process:
Making
the paste
- Pigment
manufacturers send bags of fine grain pigments to paint plants. There, the
pigment is premixed with resin (a wetting agent that assists in moistening
the pigment), one or more solvents, and additives to form a paste.
Dispersing
the pigment
- The paste
mixture for most industrial and some consumer paints is now routed into a
sand mill, a large cylinder that agitates tiny particles of sand or silica
to grind the pigment particles, making them smaller and dispersing them
throughout the mixture. The mixture is then filtered to remove the sand
particles.
- Instead of being processed in sand mills, up to 90 percent of the water-based latex paints designed for use by individual homeowners are instead processed in a high-speed dispersion tank. There, the premixed paste is subjected to high-speed agitation by a circular, toothed blade attached to a rotating shaft. This process blends the pigment into the solvent.
Figure 2:
Manufacturing process of paint
Thinning
the paste
- Whether
created by a sand mill or a dispersion tank, the paste must now be thinned
to produce the final product. Transferred to large kettles, it is agitated
with the proper amount of solvent for the type of paint desired.
Canning
the paint
- The
finished paint product is then pumped into the canning room. For the
standard 8 pint (3.78 liter) paint can available to consumers, empty cans
are first rolled horizontally onto labels, then set upright so that the
paint can be pumped into them. A machine places lids onto the filled cans,
and a second machine presses on the lids to seal them. From wire that is
fed into it from coils, a bailometer cuts and shapes the handles before
hooking them into holes precut in the cans. A certain number of cans
(usually four) are then boxed and stacked before being sent to the
warehouse.[1]
Problems and solution in technical and
engineering way:
A recent regulation (California Rule 66) concerning
the emission of volatile organic compounds (VOCs) affects the paint industry,
especially manufacturers of industrial oil-based paints. It is estimated that
all coatings, including stains and varnishes, are responsible for 1.8 percent
of the 2.3 million metric tons of VOCs released per year. The new regulation permits
each liter of paint to contain no more than 250 grams (8.75 ounces) of solvent.
Paint manufacturers can replace the solvents with pigment, fillers, or other
solids inherent to the basic paint formula. This method produces thicker paints
that are harder to apply, and it is not yet known if such paints are long
lasting. Other solutions include using paint powder coatings that use no
solvents, applying paint in closed systems from which VOCs can be retrieved,
using water as a solvent, or using acrylics that dry under ultraviolet light or
heat. A consumer with some unused paint on hand can return it to the point of
purchase for proper treatment.
A large paint manufacturer will have an in-house
wastewater treatment facility that treats all liquids generated on-site, even
storm water run-off. The facility is monitored 24 hours a day, and the
Environmental Protection Agency (EPA) does a periodic records and systems check
of all paint facilities. The liquid portion of the waste is treated on-site to
the standards of the local publicly owned wastewater treatment facility; it can
be used to make low-quality paint. Latex sludge can be retrieved and used as
fillers in other industrial products. Waste solvents can be recovered and used
as fuels for other industries. A clean paint container can be reused or sent to
the local landfill.[2]
Pigments:
Pigments are finely ground natural or synthetic,
insoluble particles used to impart color when added to paints and coatings
formulations. They are also used to impart bulk or a desired physical and
chemical property to the wet or dry film. [3]
Classifications: Some of the main
pigment classes include:
Ø Organic pigments
Ø Inorganic pigments
Ø Functional pigments
Ø Special effect pigments
While organic
pigments do not
disperse easily and form agglomerates (clumps of pigment particles), inorganic
pigments get
more easily dispersed in the resin. Functional fillers impart a desired
property to the coating like corrosion inhibition and special
effect pigments create
optical effects like metallic, hammer finish and diverse color perceptions
depending on the angle.[3]
Manufacturing:
Raw materials:
Ø Ilmenite
Ø H2SO4
Process:
In this method ilmenite was treated with concentrated
H2SO4 at 110–120°C to form ferrous and titanyl sulfates:
FeTiO3 + 4H+ → Fe2+ + TiO2+ +
2H2O
Figure 3: Production
of TiO2 pigment by the sulfuric acid process
The reaction is conducted in large concrete
tanks lined with acid resisting brick, heated by direct injection of high
pressure steam or in a pug mill. The solidified mass produced in the reactor at
the end of the reaction was then discharged from the reactor by dissolution in
water or dilute acid. After removing the insoluble residue by filtration, the
solution containing 120–130 g/L TiO2 and 250–300 g/L FeSO4 was concentrated
under vacuum at 10°C to crystallize FeSO4·7H2O which was then centrifuged.
Titanium oxide is then precipitated from solution by dilution and seeding
resulting in the formation of dilute H2SO4 for disposal.[5,6]
Chlorination method
In this method pigments are produced by direct
chlorination of ilmenite ore, separation of products by fractional
distillation, then oxidation of TiCl4.
Figure 4: Simplified
Du Pont process for pigment production from ilmenite
2FeTiO3 + 7Cl2 + 3C → 2TiCl4 + 2FeCl3 + 3CO2
TiCl4 + O2 → TiO2 + 2Cl2
The problem of this process is recovery of
chlorine from ferric chloride or marketing the large amounts of this
co-product.[6]
Electric furnace process
The ore was mixed with a certain amount of anthracite
which was just enough to reduce the iron oxide component of the ore, then
charged in an electric furnace at 1 650°C where iron oxide is reduced to
metal while titanium is separated as a slag. The reactions taking place during
reduction are the following:
Figure
5: Electric furnace process for iron separation
FeTiO3 + C → Fe + CO + TiO2(slag)
Fe2O3 + 3C → 2Fe + 3CO
The reduction of the iron oxides is not taken
to completion so that some iron oxide is left in the slag to decrease its
melting point. Melting point of TiO2 1840°C and ilmenite 1435°C.
Titanium slag
was used only for making pigment by the sulfuric acid process. The slag was
treated in the same way as ilmenite with the exception that no separation of
ferrous sulfate was necessary because the bulk of iron was already separated by
reduction in the earlier step. The sulfuric acid treatment process of the slag,
however, still suffered from the disposal problem of the waste acid and as a
result it was abandoned in the 1980s and replaced by a new technology based on
upgrading the slag to 94.5% TiO2 by leaching away most of the impurities by HCl
under pressure to render it suitable for chlorination.[6]
Figure
6: Leaching of titanium slag for production of TiO2
pigment, now obsolete
Pigment Dispersion:
High quality coatings of high
brilliance and color strength are characterized by:
- A perfect pigment dispersion
- Optimal pigment particle size
- Long-term stabilization of the dispersed particle in the
formulation.
The dispersion process consists of the
permanent breaking down of agglomerates into, as far as
possible, primary particles. There are four
aspects to the dispersion process:
Figure 7:
Pigment Dispersion
- Deagglomeration – The
Breaking down of the agglomerates and aggregates by the mixture of
crushing action and mechanical shearing force.
- Wetting – It occurs at the surface
of a pigment when a surface active agent sticks to the pigment's surface
and acts as a connection between the pigment and the binder.
Wetting out time depends on the viscosity. Heat produced by the mechanical shearing process causes the temperature of the mixture, hence reduces the viscosity, thus helping the wetting out process. - Distribution – It
demands the pigment to be equally dispersed throughout the binder system.
A lower viscosity tends to lead to a more even pigment distribution.
- Stabilization – It
prevents the pigments from re-agglomerating. The pigment dispersion is
stabilized by dispersing agents in order to prevent the formation of
uncontrolled flocculates. The resultant suspension is stabilized due to
the adsorption of binder species or molecules at the pigment surface.[3,4]
Factors influencing pigments performance:
Performance of a pigment can be measured by
the following properties:[3]
- Color of a pigment
- Color strength
- Heat resistance
- Light fastness
- Weather stability
- Insolubility
- Opacity/ hiding power
- Transparency
- Chemical stability
Color of Pigment
The color of a pigment is mainly
dependent on its chemical structure, which is determined by the selective
absorption and reflection of various wavelengths of light at the surface of the
pigment.
Colored pigments absorb part of all the wavelengths of light. For example:
- Blue pigment reflects the blue wavelengths of the incident white
light and absorbs all of the other wavelengths. Hence, a blue car in
orange sodium light looks black, because sodium light contains virtually
no blue component.
- Black
pigments absorb almost all the
light.
- White
pigments reflect virtually all the
visible light falling on their surfaces.
- Fluorescent
pigments have an interesting
characteristic. As well as having high reflection in specific areas of the
visible spectrum, they also absorb light in areas outside the visible
spectrum (ultra-violets that human eye cannot detect), splitting the
energy up, and re-emitting it in the visible spectrum.
Hence, they appear to emit more light than actually falls upon them, producing their brilliant color.
Color Strength
Color
strength (or tinctorial strength) must be considered when choosing a pigment.
Color strength is the facility with which a colored pigment maintains its
characteristic color when mixed with another pigment. The higher the color
strength, the less pigment is required to achieve a standard depth of shade.
Chemical Structure
It is one of
the factors that influence the color strength of a pigment.
- In organic pigments, color strength depends on the ability to
absorb certain wavelengths of light. Highly conjugated molecules and
highly aromatic ones show increased color strength.
- Inorganic pigments that are colored due to having metals in
two valency states, show high color strength. In contrast, those that have
a cation trapped in a crystal lattice are weakly colored.
Particle size
Particle size also influences the color
strength of a pigment. Higher color strength is obtained with smaller
particles. Manufacturing conditions are the main factor that influences the
particle size of pigment crystals. Pigment manufacturers play a crucial role.
They can:
- Reduce the size of the particles by preventing the growth of
crystals during synthesis
- Increase color strength by efficient dispersion
Pigment dispersion also plays a major role in
the color strength of the paint. Indeed, it imparts colloidal stability to the
finer particles, avoiding their flocculation and using their full intrinsic
color strength.
Heat Resistance
Few pigments degrade at
temperatures normally associated with coatings. However, at higher
temperatures, pigments become more soluble and shading can occur. Thus, for
organic pigments, heat stability is closely related to solvent resistance.
Light Fastness
Light fastness is evaluated in
relation to the whole pigmented system, not just the pigment. The binder imparts
a varying degree of protection to the pigment, so the same pigment will tend to
have better light fastness in a polymer than it will in paint.
Other pigments that may influence light fastness in a pigmented system. These
include:
- Titanium dioxide promotes the photodegradation of most
organic pigments. Therefore, high ratios of titanium dioxide lead to
poorer levels of light fastness.
- Iron oxide can improve the light fastness of organic
pigments, due to the fact that it is an effective absorber of UV light.
When the association of two pigments gives a
better light fastness, it is called a synergistic effect and when the light
fastness obtained is lower, it is called an antagonistic effect.
Weather Stability
For
outdoor applications, pigments used for coloring should be selected for their
weather resistance characteristics. The selection of pigments for outdoor use
depends on:
- Outdoor
performance required (life time, climatic region/ Kilo Langley)
- Binder type
- Concentration
of the pigment
- Presence of
titanium dioxide (which typically accelerates fading)
- Concentration
and type of light stabilizers used
Insolubility
A pigment must be insoluble in the vehicle (the medium in which it
is dispersed), and it must not react with any of the components of the paint,
such as crosslinking agents.
Pigments are required to retain these properties even when the paint is being
dried, which is frequently carried out at elevated temperatures. Once in the
dried film, the pigment must also remain unaffected by the substrate and to
agents with which it comes into contact, including water, which may simply be
in the form of condensation, or acidic industrial atmospheres.
Opacity/ Hiding
Power
Hiding power is the ability of a pigmented
coating to obliterate the surface. It is dependent on the ability of the film
to absorb and scatter light. Naturally, the thickness of the film and the
concentration of the pigment play a fundamental role. The color is also
important.
Chemical Stability
Resin,
crosslinking agents, UV-initiators, and any other additive may react with the
pigment and alter its performance.
Problems and solution in technical and engineering way:
Solubility of a pigment generates the
following problems:
- Blooming - If the pigment dissolves
in the solvent, as the paint dries, the solvent comes to the surface and
evaporates, leaving crystals of the pigment on the surface in the form of
a fine powder. As solubility increases with temperature, this phenomenon
is made worse at elevated temperatures.
- Plate out - The effect of plate out looks
similar to blooming, but occurs in plastics and powder coatings. However,
it is not due to the pigment dissolving, but rather to the surface of the
pigment not being properly wetted out. It usually occurs mainly with complex
pigments and once wiped from the surface does not reappear.
- Bleeding - Pigments in a dried paint
film may dissolve in the solvent contained in a new coat of paint applied
on top of the original film. If the topcoat is a different color,
particularly a white or pale color, the result can be disastrous. Again
elevated temperatures exacerbate the problem.
- Recrystallization - This
phenomenon was almost unknown until the introduction of beadmills. During
the milling stage, heat is generated, which dissolves a portion of the
pigment. Over a period of time, the dissolved "pigment" starts
to precipitate out, loses brilliance and color strength. This becomes
especially noticeable in the case of paints containing two differently
colored pigments that have different solubility characteristics. The more
soluble pigment dissolves and then as it comes out of solution and
precipitates, the paint will take the shade of the second pigment.
Recrystallization can even take place in aqueous systems. It can be
avoided by using less soluble pigments and/or by controlling the
temperature during the dispersion process.[3]
Another adverse effect can come from:
Chemicals that the coating gets in contact
with. Water, in the form of condensation, can seriously affect a paint film,
particularly in bathrooms and kitchens. Many of the detergents used for
cleaning paintwork are harsh and have an abrasive affect upon the pigment.
Should the coating come into contact with food, it is essential firstly, that
the coating is unaffected and secondly, that the food remains unchanged.[5]
References:
1. http://www.madehow.com/Volume-1/Paint.html
2. https://www.essentialchemicalindustry.org/materials-and-applications/paints.html
3. https://coatings.specialchem.com/selection-guide/pigments
4. Habashi
F (1993) A Textbook of Hydrometallurgy (2ndedtn). Métallurgie Extractive
Québec, Québec City, Canada
5. Habashi
F (1996) Pollution Problems in the Mineral and Metallurgical Industries,
Metallurgy Extractive Quebec, Quebec City.
6. https://www.oatext.com/Ilmenite-for-pigment-and-metal-production.php
7. https://en.wikipedia.org/wiki/Ceramics_industry_in_Bangladesh
8. Ceramic
Industry of Bangladesh: A Perspective from Porter’s Five Forces Model-Nusrat
Jahan Volume– V, Issue– 02, July-December, 2010
9. https://solutionsinmotion.clevelandvibrator.com/eight-steps-of-ceramics-processing-and-industrial-vibration/
10. https://www.slideshare.net/hzharraz/ceramics-32994025
أزال المؤلف هذا التعليق.
ردحذفI might want to say this is a very much informed article as we have seen here. Your approach to composing is exceptionally great and furthermore it is a valuable article for us. Gratitude for sharing an article like this.Caluaine Muelear Chemical Manufacturer
ردحذف